
Specification
1. What is a Globe Valve used?
Globe valves are used to regulate flow in a pipeline and it is a linear motion valve. It operates with a handwheel and by simply rotating the handwheel, the flow rate can adjust to any desired level. The disc acts to remove the flow path or completely close the flow path. A Globe valve is employed to control the system flow. The pressure drop and flow rate control must be taking care of in the design to avert premature failure and assure satisfactory valve performance. The maximum differential pressure across the valve disc is less than 20% of the maximum upstream pressure.
The following are some of the standard applications:
-
Fuel oil system where regulated flow and leak tightness is important.
-
High-point vents and low-point drains where leak tightness is the major considerations.
-
Chemical feed and extraction drain systems.
-
Cooling water systems application.
-
Main steam vents and drains, boiler vents and heater drains.
-
Turbine lube oil system.
2. How does a Globe Valve work?

ANSI 150# Cast Steel Flange End Globe Valves
Globe valve design comes with a disc that translates against a seat and the fluid flow according to the direction arrow engraved on the globe valve body. The arrow defines the flow direction before valve installation. The seat is in the valve middle and parallel to the pipe. The opening in the seat will cause closing off with the disc. When the handwheel is turned manually, the disc is lowered or raised by the valve stem. The fluid flow is shut off when the disc is fully lowered and the fluid flow is at a maximum rate when the disc is fully raised to the top. The fluid flow is regulated with partial to the vertical travel of the disc when the disc rises to less than the maximum level.
There is a high level of head loss due to the design of the angle in the globe valve body. The head loss refers to the measurement of the reduction in the total head of liquid as it moves through the system. To calculate head loss, summing the elevation head, velocity head, and pressure head. Head loss is inescapable in a system. It is usually increased by discontinuities or obstructions in the flow path such as S-Shape globe valve design. The pipes should fix in a constant area in order to avoid additional pressure losses at high pipeline velocity.
Globe valve has common three main body types which are angle design, Y-shaped design, and Z-shaped design. The Z-body globe valve design is the most simplest and common use in the water system application and is known as a straight-through globe valve. It has a Z-shaped diagram design or partition across the globular body and it contains a seat in the middle bottom body. The seat is horizontal and the disc and stem travel at right angles to the pipe axis. The stem passes through the bonnet.
3. What is the difference between a Gate Valve and a Globe Valve?
There is a comparison between globe valve and globe valve and here are the differences:
-
Applications: The globe valve is suitable to apply when massive changes in system pressure and the valve design are unidirectional. While gate valve is suitable for low pressure drops application.
-
Structure: Gate valve and glove valve have a similar outlook. However, the gate valve has a simpler construction design and its internal components are located on the top part of the valve body. The body becomes hollow when the valve turns on and it caused a little pressure drop overall. On the contrary, the gate has a primary purpose to regulate and provide a positive shut-off function. The globe valve design allows changes in flow rate and flows direction that contributes to a high-pressure dropping.
-
Function: Gate valve is designed as isolation of media and it can’t manage the strength of media flowing in a partially open position. Globe valve has better flow rate control.
-
Valve Operation: The disc lodges between the seats as a gate valve working mechanism. The flowing movement can be either full flow or no flow at all. The valve flow space is big as the cavity with little extra where the stem globe valve and seats are located when the valve is at the opening location. The globe valve disc shifts aligned to the media flow. The disc has to move a little from the seat to create a full flow rate.
4. What is the difference between a rising stem and a non-rising stem Globe Valve?
There are two types of globe valves, rising stem globe valves, and non-rising stem globe valves. Rising stem globe valves are operated by pulling or pushing the valve stem upwards and it requires more space compared to the non-rising stem. The round handle rotates a threaded stem that is attached to the middle body. The stem is rising by turning the handle and the valve is in an open position. The globe valve is easy to tell if the valve is closed or open by observing the amount of stem that is exposed on top of the handle. The globe valve is at the closing position when there is no exposed stem.
The rising stem globe valve is fully open when the handwheel is rotated more than 360 degrees to the left and fully closed when the handle rotates to the right. The advantage of a non-rising stem is where space is limited or tight and both valve options are applicable. For example like underground pipelines. The disadvantage of a non-rising stem is the screw threads that lift the disc are exposed to the fluid being controlled by the globe valve. It causes system problems if the fluid tends to foul the thread and a non-rising stem globe valve is usually applicable in clean liquids and gases.

Threaded End SS316 Globe Valves 200PSI
5. What are the important things to take note of when installing a Globe Valve?
The Globe valve is unidirectional and the body arrow of direction is easily checked by looking into one end of the valve. The globe valve usually is installed vertically to keep the handwheel operating at the top of the valve. This ensures no premature wear or damage that will affect valve operation.
The globe valve comes with different working pressure and does not exceed 100% maximum pressure rating during system operation. Pressure fluctuations beyond the valve's actual working pressure can cause system failure and high maintenance costs.
Regular inspection and maintenance schedule will increase the valve lifespan. Check every single component to ensure consistent valve performance. Check regularly the disc and seat if the valve is not operating regularly. If the valve packing is loosened, slightly fasten the gland bolts and do not overtighten. Replace a gland packing if the external leakage can trace by human eyes. Before the valve is uninstalled, ensure there is no pressure in the pipeline and it has cooled to room temperature.
HOW TO INSTALL A GLOBE VALVE

*** The globe valve operates by clockwise close and please do not overtighten on the seat to close.
STEP 1
Remove debris or packing from the globe valve surface.


STEP 2
Measure the valve installation space and ensure the space is enough to turn the handwheel.
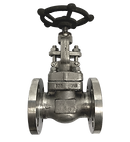
STEP 3
Complete the valve dry cycle from open to close position and repeat a several times.

STEP 4
Insert a gasket and install it in parallel to the flanges.
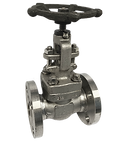
STEP 5
Insert the hex bolt in the selected bolt hole and align two pieces of flanges.

STEP 6
Tighten the flange with hex bolts and hex nuts gradually in a diagonal balance pattern.
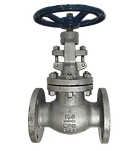
STEP 7
Operate the globe valve from lower pressure to test the overall valve performance.