
Specification
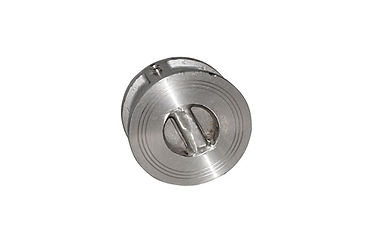
1. What is Dual Plate Check Valve?
Dual plate check valve is a compact valve design. It has advantages over other types of check valves in terms of size, weight, cost, ease of installation, and service maintenance. The middle plate works independently of each other and the torsion springs shut the valve quickly to minimize reversal flow and prevent system water hammer. They are fitted for different applications such as manifolds, flowlines, pipeline transmission and distribution, metering runs and pressure regulation, underground storage systems, and general pipeline application.
The valve required a low force to push the plates. The design is single-piece body construction with a flange end connection. There is a total of four pits in the body of the dual plate check valve that is used to insert the stop pin and hinge pin. It employs two spring-loaded plates hinged on a middle hinge pin. The plates close by the action of stainless steel torsion spring before flow reversal takes place when the flow is reduced. The standard valve is shipped with a plate in a fully closed position.
The dual plate check valves are used to help keep the operating facilities running smoothly and it is applied in many industrial applications:
-
Refining
-
Marine
-
Mining
-
Offshore
-
Petrochemicals
-
Fossil, Nuclear & Cogeneration Power
-
Water application
The benefits of dual plate check valve:
Cost Saving design:
Compare to the conventional full-bodied type, the inherent design dual plate results in significantly reduced weight. The dual plate check valve can be as one-fifth the weight of the equivalent full-bodied valve unit when the size body gets larger. This helps in saving in initial cost, space, and pipeline support element installation.
Reduced line shock:
Dual plate check valve must close as quickly as possible prior to the flow having the opportunities to reverse in order to eliminate or minimize pipeline shock. The half piece of plate from a full-bodied check valve reduced the fluid drag and the fluids move more quickly to the closing position. The swing radius is one-half that the flow of the conventional check valve and it leads edge distance from open to the closed position is halved and in turn reducing the travel time by 50%.
By having the lighter weight of dual plate check valve, it has a major advantage in minimizing slamming and water hammer. The heavier valve bodied has larger momentum when swinging closed. It caused a slam into the valve seat.
2. The Dual Plate Check Valve operation mechanism

The dual plate check valve comes with double combine semi-circular D-design plates loaded attached with stainless steel torsion spring and hinged on middle hinge pins. So that they can swivel freely about the axis of the hinge pin and the hinge pin with the spring and plates are supported by two brackets on either side and seated on the dual plate check valve body.
To prevent the closure plates from sagging beyond the desired opening, the body brackets retain the stop pin provided above the hinge pin. The hinge and stop pin, stainless steel torsion spring, and closure plates are assembled with the bracket. The whole assembly is lifted and placed parallel to the body's bottom rib. Next, it moves to 90 degrees such that the brackets are located below the lug provided in the body. The bracket carrying the whole assembly was retained by the lug by using screws. Bearing washers are provided in between the plates for smooth swiveling action. To prevent the motion of the spring inside the body, spring bearings are provided.
Dual Plate Check Valve
3. Is Dual Plate Check Valve Non-slam type?
The dual plate check valve is classified as a non-slam design. The two plates are hinged in the center vertically for horizontal installation. It is altogether eliminating the effect of gravity. The momentum developed when they move to the closed position. The valve closes as the flow velocity approaches zero and before the flow reversal is further due to spring-assisted closed. When it starts closing, the flow cushions the plates and seat and hence minimizing valve slamming.
Water hammer is the least existent in dual plate check valves as the backflow pressure does not affect the valve performance when it is at the closing position. Each plate being half size provides a straight flow path and offering the least resistance. The valve closure starts as soon as flow velocity reduces and thereafter the closing rate flows the flow velocity reduction pattern. The valve closes when the flow velocity approaches zero before the flow reverses. This is the process of how the water hammer is being eliminated.
4. How do you maintain a Dual Plate Check Valve?
It is recommended to do a periodic inspection and valve maintenance in order to enhance the life of the dual plate check valve for better operability. Insufficient flow, improper installation, turbulent flow, and valve location to the pump will cause severe damage to internal part components of the dual plate check valve. During installation, the improper alignment of valve and pipe can lead to unbalance tightening or out of torque value of both flanges installation which may cause excessive stress on the bolts and nuts and next lead to system leakage.
There is some common problem during or after installation and here is the troubleshooting list:
HOW TO INSTALL A DUAL PLATE CHECK VALVE

*** Please take note that the valve should be installed a minimum of 5 pipe diameters downstream of any piping components such as valve or fittings to allow the flow to stabilize without interruption. To allow the system pressure recovery, there should be a minimum of 2 diameters of straight piping downstream of the valve before the next fitting installation.
STEP 1
-
Refer to the arrow sign attached to the valve body for preferred flow direction.
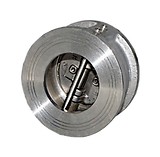
STEP 2
-
Clean the valve flanges and remove protective grease from the valve body and flange connection. Clean the valve interiors adjacent piping before valve piping joint mounting.

STEP 3
-
Ensure all surfaces cleanliness and other internal part surfaces. The surface must be clean and free of debris before installation.
-
Before installation, check and ensure the valve is in a fully closed position.
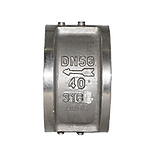
STEP 4
Align the bolt holes of the flange end connection with the piping flange and insert the gasket before tightening the bolts and nuts. Flange bolts and nuts shall be tightened evenly.

STEP 5
Lubricate the bolt for ease of installation.
